Case Study 5 : Auto Parts Manufacturer
Auto Parts Manufacturer Chooses Asprova For Its Good User Interface
Reduces Labor of Adjusting The Schedule
-Auto Parts Manufacturer –
An auto parts manufacturer had been using a custom-made scheduler running on DOS before switching to Asprova. As the number of products and the required number of production lots in their factory increased, they eventually exceeded the capability of the scheduler, and were forced to limit the number of products and to break orders into several groups to be scheduled in separate scheduling runs. Other problems, such as the inability to restrict color for each facility, worsened this scheduler’s usability. After introducing Asprova, they became able not only to schedule all of the products simultaneously, but also to automatically assign jobs, taking into account the color restriction of each facility. These improvements, along with the ease of rescheduling using the Gantt chart, have considerably reduced the labor of adjusting the automatically generated schedules.
Problems Prior to Introduction
- Inadequate data processing capability of the existing custom made scheduler, leading to impracticalities such as having to limit the number of products and divide orders into several scheduling runs
- Numerous typing misses when manually scheduling products that were left out of the schedule
- Inability to restrict colors in each facility, leading to inevitable manual schedule modification by an experienced schedule manager
Reasons for Introducing Asprova
- Ease of understanding the schedule in Gantt chart form
- Ease of modifying the schedule by drag-and-drop on the Gantt chart
- Ability to restrict colors in each facility
Benefits of Introduction
- Enabled all products to be scheduled simultaneously.
- Enabled scheduling of many times the original data size in the same amount of time.
- Reduced schedule adjustment work due to the ability to restrict colors in each facility.
- Standardized most of the scheduling work, by codifying schedule managers’ know-how in the form of master data set into Asprova.
A System That Became Practically Useless
Before introducing Asprova, the auto parts manufacturer had been using a custom-made scheduler running on DOS. But because the processable number of lots was inadequate, their increasing number of finished products and their increasing number of production lots eventually exceeded this scheduler’s data processing capability. Consequently, the factory had to artificially limit number of finished products, and divide the orders into groups that they scheduled in separate scheduling runs. This became quite a burden. Products that were left out at the schedule would be handled manually, but, as one manager said, “Manual scheduling was prone to typing errors and many other problems.” Furthermore, diversification in the color of the products made it crucial to have a color restriction function in the schedule. But since the custom-made scheduler did not have that function, an experienced schedule manager would inevitably have to modify the schedule manually. Considering these problems, the manager says that the custom-made scheduler had become “practically useless.”
They did think about ways to improve the existing custom-made scheduler, but as one of the managers said, “With the year 2000 at hand, introducing a scheduling package was much better than going through the hassle of improving the system.”
After initially fruitless efforts in finding a package that would match their needs, they then found out about Asprova, and immediately requested a demonstration. Besides having the ability to restrict colors for each facility, “[Asprova’s] GUI is incredibly easy to understand visually, and the ability to correct schedule using a mouse is just amazing,” said one astonished manager. After learning more about Asprova’s functions by using a trial version of Asprova and attending a training seminar, they decided to introduce Asprova.
Reduces Labor of Adjusting The Schedule
It was recommended that initial implementation work, such as workers’ education, creation of the master data based on schedule managers’ knowledge, and development of peripheral functions, were to be done mainly by the company itself, with the support of the distributor International Laboratory Corporation. Development of peripheral functions was done in parallel with the test run. However, as one manager noted, designing and altering the functions to meet the demands from the production site was not easy.
Since the installation of Asprova, they have not only become able to schedule all of the products simultaneously, but they can now create this complete schedule in the same amount of time it took to create one of the partial schedule before, which had only included a fraction of the total data set. Regarding the time required to make a working schedule, one manager explains, “Since Asprova automatically creates a schedule that takes into account the color restriction of each facility, we don’t need to do nearly as much adjusting work.” What’s more, they have been able to standardize most of the scheduling work by codifying schedule managers’ know-how in the form of master data that was set into Asprova at the initial installation. In addition, while it has previously been difficult to explain the procedure for scheduling to new employees, this has became much easier because of how simple it is to verify and modify the schedule using Asprova’s Gantt chart.
In the future, the company intends to transmit the schedule directly to facilities, to expand the number of processes in the schedule, and to meet various needs of the production site by more effectively using Asprova and by developing peripheral functions. Additionally, in developing the peripheral functions, the company plans to built an even easier-to-use system by reconstructing the utility in Microsoft Access and using Asprova plugin architecture.
Figure 1: System Configuration
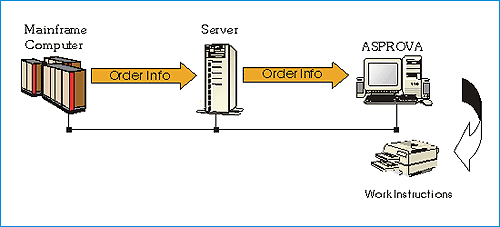
Scheduling is performed based on order data from the mainframe computer. Asprova’s master data is entirely created on the PC. A daily report is generated after scheduling.
Figure 2: Gantt chart created from scheduling with Asprova.

Product specifications are made easy to understand by intelligent use of colors.
Figure 3: Customized screen of Asprova Utility

A variety of needs from the production site are reflected.
Data Volume | |
---|---|
Finished products | 60 |
Total items | 60 |
Resources | 46 |
Processes | 1 |
Scheduling period | 3 days |
Scheduling cycle | once/day |
Lots in scheduling period | about 3,000 |
Jobs in scheduling period | about 3,000 |
Chooses Asprova for its excellent user interface Reduces labor of adjusting the schedule Read More… |