Case Study 3 : Auto Parts Manufacturer
Auto Parts Manufacturer Reduces Inventory and Achieves Consistency Among Process Plans
“Asprova” a Byword For Production Planning Throughout the Factory
-Shonan Unitec Corporation –
Shonan Unitec Corporation specializes in production of auto parts such as pedal assemblies, pulleys, press parts for cabs, as well as various other products such as sound barriers, pedestals, etc. Before the introduction of Asprova, schedules were prepared separately for each process based on documents generated by the mainframe computer. This caused mismatches between processes and excess inventory for each process, resulting in long overtime work. Now, after introducing Asprova, they are able to make consistent schedules by visually checking how much load is applied or required, enjoying various benefits such as reduction of inventory and workload. When it comes to production planning, everyone in the factory thinks of Asprova.
Problems Prior to Introduction
- Inconsistency between processes and excess inventory from having different staff members prepare schedules for each process based on documents generated by the mainframe computer
- Long overtime work required to complete items by their due dates, putting heavy load on the workers
- Daily overtime work for the person in charge of planning to adjust the schedule
Reasons for Introducing Asprova
- Asprova’s ease of installation
- Asprova’s diverse standard features
- Asprova’s bulk production capability
Benefits of Introduction
- Achieved consistency between processes, enabling smaller lot sizes and reduction of excess inventory, which could now be managed visually.
- Improved the accuracy of the master data and the schedule, enabling reduction of the load on workers.
- Allowed the schedule to be created by one employee alone, rather than by two or more employees working overtime.
- Made it easy for the factory to increase the number of manufactured item types.
Inconsistent Scheduling Among Processes
Shonan Unitec Corporation used to output documents to each process once a week, generated based on orders from customers using a standard lead time. These were calculated by a mainframe computer without checking the load on the equipment. Although each process was managed by scheduling specialists who worked out weekly schedules relying on their intuition and experience, processes were inconsistent because they were scheduled independently of other processes. This led to awkward situations in which produced parts were not used for a long time or production stopped for lack of necessary parts. Each process center would have to hoard inventory for fear of item shortages. If there was a sudden change in schedule or inconsistency between processes, they had to work overtime to finish the lot in time for the customer’s due date. Scheduling managers also worked overtime everyday adjusting the schedule to flatten the workload of the factory floor.
To resolve these problems, they looked into introducing a scheduling package that would enable “scheduling that takes into account the load on facilities for all the processes.” The factory wanted to select a package that was easy to install, capable of leveraging the data and capabilities of the existing system, and equipped with all required capabilities. In addition to load leveling throughout the processes, they needed the capability to assign lots for the press process combining multiple customer orders. According to Kenji Saito of the System Group, when they evaluated Asprova, they saw no problem regarding ease of installation, and concerning functionality, “when we had looked into Version 3, it had still been lacking in features, but when we heard that Version 4 had a bulk production feature we were impressed.” Following this evaluation, they decided to introduce Asprova.
Asprova a Byword For Production Planning
The factory’s System Group and the Factory Works Group played the central role in introducing Asprova. International Laboratory Corporation (ILC), an Asprova distributor, helped with the installation work several times a week. “Although it was hard to create new data that we had not used before,” says Haruo Kasama, Factory Works Group, “we were able to start actual operation in a relatively short period of four months.” During the early stage of actual operation, data was not very accurate. “We received a lot of complaints if there were problems with a schedule,” says Saito. “But now,” Kasama explains, “the situation is completely different from how it was in the early stage of introduction.” The accuracy of the master and scheduling has been improved a great deal because they corrected data every time they received complaints.
As a result of introducing Asprova, they have been able to achieve consistency between processes, which was one of their initial objectives. This improved the operation of the factory floor, enabling a reduction in the size of production lots. “Inventory quantity has reduced significantly and housekeeping is now properly performed,” Saito says. Scheduling used to be performed by several people but now can be done by one person alone, resulting in substantial savings in man-days. The load on the factory floor has also been considerably reduced because the accuracy of scheduling has been improved to balance the amount of work for each day. Recently, items which were previously manufactured in other factories are being moved over to the main factory, but they have had no trouble in managing the increased production.
Now, says Saito, everyone in the factory thinks of Asprova when it comes to production planning. The factory floor counts on Asprova and makes numerous requests. These requests are being met one by one with the cooperation of ILC Corporation. In the future, Shonan Unitec plans to improve the mainframe as well as upgrade Asprova to better meet requests from the factory floor.
Figure 1: System Configuration
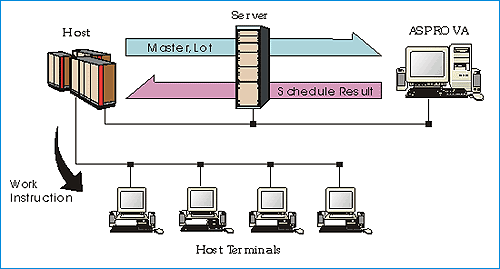
The mainframe sends data to Asprova via a server and Asprova returns the result of scheduling. The mainframe then sends production instructions to terminals at each process.
Figure 2: Gantt chart showing the result of assignment using the bulk production capability

Figure 3: Aggregated list taken from Asprova’s time series data using a Microsoft Access query

Schedule data stored on the server may be accessed from PC terminals.
Data Volume | |
---|---|
Finished products | 10,000 |
Total items | 20,000 |
Resources | 150 |
Processes | avg. 3 |
Scheduling period | 3 weeks |
Scheduling cycle | daily |
Lots in scheduling period | 1,200; 6,200 |
Jobs in scheduling period | 10,000; 60,000 |
Shonan Unitec Corporation
Since its establishment, Shonan Unitec Corporation has manufactured auto parts such as pedal assemblies (accelerator, brake, and clutch), pulleys, press parts for small-sized, medium-sized, and large-sized cabs, as well as various other products such as sound barriers, pedestals (base parts for construction), etc.
Left to right: |
Reduces inventory and achieves consistency among process plans “Asprova” a byword for production planning throughout the factory Read More… |
![]() |