Case Study 2 : Electric Manufacturer
Electric Manufacturer Chooses Asprova for GUI and Rich Features
Shortens Planning Cycle and Improves Scheduling Process
-Mitsubishi Electric Corporation, Nakatsugawa Works –
Mitsubishi Electric Corporation’s Nakatsugawa Works specializes in the manufacture of ventilation fans for home and business use, ventilating air cleaners, and industrial blowers. Prior to the introduction of Asprova, schedules were prepared through weeks of manual labor based on lists of processing jobs generated by the host computer in ignorance of the capacity of machines in the factory. However, as a result of the introduction of Asprova, the time required to prepare schedules has been reduced, and the cycle over which the processing plans are output by the host computer has been shortened. The benefits of introducing Asprova have been so apparent that it is now being used in 5 divisions within the Nakatsugawa Works.
Problems Prior to Introduction
- Inordinate time required for workgroup leaders to draft schedules by based on one-month processing plans output by the host computer
- Unnecessary setup time and simple errors resulting from the manual scheduling
Reasons for Introducing Asprova
- Asprova’s user-friendly GUI
- Asprova’s large number of standard features
- Asprova’s fast scheduling speed
Benefits of Introduction
- Reduced time workgroup leaders spend preparing schedules, allowing them to undertake other tasks, such as following up on component delivery dates and processing vouchers.
- Eliminated the problems of unnecessary setup time and simple scheduling errors.
- Enabled more frequent outputting processing plans from the host for more flexibility in host-side planning changes, without adverse effect on the preparation of processing schedules.
Planning Requires Enormous Work
At Mitsubishi Electric Corporation’s Nakatsugawa Works, schedules are drafted for two sets of processes: component processing and product assembly processes. Prior to the introduction of scheduling software, lists of infinite-capacity processing jobs corresponding to assembly schedules for the next month were output twice a month from the host computer to each workgroup. Each workgroup leader would refer to these infinite-capacity lists while attempting to manually prepare finite-capacity processing schedule, taking into account conditions such as standard times, operating times, setup times, etc. It was also necessary to respond to changes in schedule, resulting in some 2 weeks of each month being taken up by schedule preparation and revision. In addition to taking a lot of time to prepare, these schedules often included unnecessary setup time and simple errors because of the huge volume of data that needed to be considered.
In order to solve these problems, Mitsubishi began to consider the introduction of a scheduling system, and Asprova was the first product they saw demonstrated. The demonstration was conducted by Tokai NTT Data Communications Systems Corporation, a certified distributor of Asprova. Mitsubishi was particularly impressed by Asprova’s high-speed scheduling, the large number of standard features, and the ease of viewing of its user interface. “We were impressed by Asprova’s scheduling functions”, says Mr. Yoji Tanaka, Director of the Manufacturing Planning Department’s System Engineering Section. In order to increase the client’s understanding of the product, Tokai NTT Data Communications Systems Corporation, with the cooperation of the staff responsible for schedule preparation, conducted a two-day demonstration using actual data. “We became confident that Asprova was the product for us”, says Mr. Takuhiro Suzumura, Chief Technician of the Manufacturing Processing Section of the Residential Ventilation Manufacturing Department. Thus, after detailed evaluation of the product by the System Engineering Section and by factory managers, the company decided to introduce Asprova.
Asprova peripheral development and installation was largely carried out by the System Engineering Section. Mr. Masakazu Kajita, an engineer in the Manufacturing Planning Department’s System Engineering Section, indicates that the collection of data and establishment of master settings was a more difficult task than that of peripheral development. “For divisions with reliable original data, the procedure takes less than a month, but where no such data exist, it is an extremely time-consuming process”. Asprova is currently being used in 5 divisions, and data are being collected and conditions determined in preparation for the introduction of Asprova to a 6th division.
Asprova Enables Shortening of Planning Cycle and Improvement of Scheduling Process
As a result of the introduction of Asprova, workgroup leaders now spend less time preparing schedules, and are able to allocate more time to tasks other than scheduling, such as following up on component delivery dates and processing vouchers. Asprova has also solved the problem of unnecessary setup time and simple errors being included in schedules, and greatly reduced the effort required to search for relevant items when making schedule modifications.
At the same time, the Nakatsugawa Works has reduced the cycle for outputting processing plans in order to respond more flexibly to planning changes on the host side. Where plans were previously output twice a month, they are now output as often as once a day for some items. This transition was effected smoothly due to the use of Asprova for schedule preparation. “We wouldn’t be able to prepare schedules on such a short cycle without Asprova”, says Mr. Suzumura. Asprova has thus been effective not only in improving the process of schedule preparation, but also in supporting improvements on the host side.
Asprova is currently being used in Mitsubishi Electric Corporation’s Nakatsugawa Works with virtually no problems whatsoever. An RDBMS has also been introduced to make effective use of the data compiled using Asprova, and is available for use from client PCs, together with applications for other peripheral functions such as inputting production results and viewing processing plans. The staff at Nakatsugawa Works are currently exploring ways of making even more effective use of Asprova data, including the introduction of a paperless system, and the use of Asprova in preparing processing schedules for the assembly line.
Figure 1: System Configuration
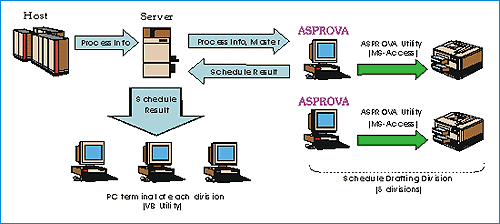
Data stored on the host computer is divided up according to workgroup and is sent via a server to the scheduling division in which each workgroup is located. Each scheduling division constructs a schedule using Asprova and outputs work directives using the Asprova Data Management Utility. Data from the schedule is also sent back to the server, where it may be accessed from PC terminals using VB utilities developed in-house.
Figure 2: Viewing Asprova Schedules

Gantt Charts and Lot Gantt Charts
Figure 3: Screenshot of VB Application Developed In-House

Schedule data stored on the server may be accessed from PC terminals.
Data Volume | |
---|---|
Finished products | 3,000 |
Total items | 7,100 |
Resources | 55 |
Processes | 1 or 2 |
Scheduling period | 3 months |
Scheduling cycle | once/month |
Lots in scheduling period | 10,000 |
Jobs in scheduling period | 20,000 |
Mitsubishi Electric Corporation, Nakatsugawa Works
Nakatsugawa Works was originally established as a branch factory of Mitsubishi Electric Corporation’s Nagoya Works, and has since been involved primarily in the manufacture of products involving wind and air, including ventilation fans for home and business use, ventilating air cleaners, industrial blowers, and hot-air heaters. Recently, Nakatsugawa Works has also been involved in the manufacture of hand driers and solar electricity generation systems for residential use.
Left to right: |
Introduces Asprova for GUI and rich features Shortens planning cycle and improves scheduling process Read More… |
![]() |