Case Study 8 : Synthetic Resin Manufacturer
Synthetic Resin Manufacturer Chooses Asprova for Processing Speed.
Now, Only One Person is Responsible for Two Factories’ Scheduling Work
-Japan Polyolefins Co. Ltd –
Japan Polyolefins Co.,Ltd. manufactures and distributes low-density, high-precision polyethylene, high-performance polyethylene, advanced synthetic resin, etc. The Oita factory of the company had been using a self-made scheduler with Artificial Intelligence capabilities, but there were problems with speed and operationality. On top of that, machine failures were really hindering their progress. After implementing Asprova, scheduling and revision work were relieved considerably. Recently, the company has also implemented Asprova on their Kawasaki factory.
Problems Prior to Introduction
- Heavy burden on scheduling managers due to irresponsive custom-made scheduler
- Unavoidable overtime work twice a month just for the routine scheduling job.
- Machine failures and Y2K problems caused by old hardware.
Reasons for Introducing Asprova
- Asprova’s speed
- Asprova’s ease of operation
- Asprova’s rich features
Benefits of Introduction
- Realized the objective of constructing a new scheduling system in a short time
- Relieved the burden on scheduling managers thanks to Asprova’s high-speed scheduling and its Gantt chart’s ease of modification
- Facility loads and job assignments can easily be viewed graphically on the Gantt chart, leading to quick customer service response
- Only one scheduling engineer is needed for two factories scheduling work, without any extra overhead time, as both factories are a part of a BPR system.
Irresponsive custom made scheduler
Before introducing Asprova, the Oita factory of Japan Polyolefins Co., Ltd. was using their own custom made scheduler, which had AI capabilities. Scheduling was based on order prospect and inventory information calculation. Manufacturing conditions, such as production process order and move time, were considered in the scheduler’s algorithm. As time passed by, the industry’s condition, manufacturing restrictions, have all changed, invalidated the scheduler’s results. While the existing custom made scheduler was capable of schedule modification and rescheduling, “…It took too long to display the result on the screen if you change quantities or move job assignments.”(Hideo Kyoizumi, assistant head manager of production management team, business group, management department). As a consequence, scheduling results had to be modified manually, leading irresponsive schedule modification and stress on the scheduling managers.
Figure 1: System Configuration
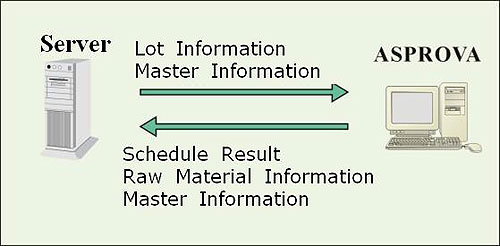
The server sends the information needed for scheduling, lot data and master data, to the client terminal hosting Asprova. The resulting schedule data, such as job data and materials data, will then be sent back to the server from the client (Asprova). Materials table uses an ADSPCSV function which will only output updated fields.
Figure 2: As we see on the BOM table, the final product is made out of three different parts

Asprova will use its bulk production function, and check inventory for availability of each part, to restrict overproduction of parts in a lot.
Figure 3: Gantt chart of resulting schedule

Item specifications data is set in the dispatching rule, and jobs are assigned according to specification order. Gantt chart coloring is set according to each item’s specification to improve readability and ease confirmation and modification.
Figure 4: Customized master maintenance screen done on Microsoft Access

Multiple basic input screens are replaced by one concise dialog. Other customization includes usage of dropdown listbox and changing default table field names to names used inside the factory.
Rapid Implementation
Realizing the need of a new scheduling system, Japan Polyefins entrusted Hitachi SC Ltd., which developed the custom made scheduler, to choose a scheduling package for them. The choice was made on the basis of the scheduling speed, ease of modification and rescheduling, and operationality issues. The fact that Asprova allows user to easily modify schedules on the Gantt chart visually and effectively, along with the processing speed of Asprova, have put Asprova on the top of the list, easily surpassing other competitor. What’s more, in addition to Asprova’s rich standard features, updates and promising new features are continually released. The implementation decision was an easy one.
Hitachi SC was responsible for Asprova implementation process and operation. There were some master data structure inconsistencies between the existing system and Asprova, so they had to put a little more effort to assure compatibility. The existing master data was changed, however, there were still troubles that resulted in errors on Asprova. They had to debug the errors one-by-one, consulting directly to Asprova Corporation on complicated issues.
In spite of these issues, the implementation process progressed beyond expectation, ending few months ahead of schedule.
Now, only one person is responsible for two factories’scheduling work
New to the system, scheduling engineers were overwhelmed by Asprova’s features and operational method. The online help file included in the package was sometimes too technical for first time users, so the engineers relied heavily on Hitachi SC’s support.
At present, one year after the implementation of Asprova, Japan Polyolefins scheduling department engineers are reaping the benefits from the seed they sowed. “Production scheduling has become so effortless,” said Konosuke Sato, Head of Production Manager Team, Business Group, Managerial Department, satisfied with scheduling burden relief that had been haunting them. The ability to modify jobs and tasks easily and intuitively on the Gantt chart, and the speed of rescheduling that Asprova provide, have a lot to do with it. They have mastered the usage of Asprova’s scheduling result and material data, resulting in faster and more reliable scheduling.
The company has another factory at Kawasaki, which is manufactuiring a same product line. The Kawasaki factory did implement a scheduling package, which can be customized using a special language unique to that program. But the scheduler was too restricting that it lacked practicality in dealing with a real world situation. A lot of time was spent in modifying scheduling results manually, and as a result, they might be better off scheduling manually in the first place. Not to mention the expensive cost of hiring specialist for programming the unique language.
Aware of the success the Oita factory was having with Asprova, Japan Polyefins decided to deploy Asprova in their Kawasaki site, and to make a major change in their organizational structure. Now, each resin type has only one scheduling engineer in charge for both factory, and the time to do one scheduling run is cut to half.
In the future, the production management department plans to exploit more out of Asprova and its new features, increasing scheduling speed as well as precision. The engineers are planning to go further. They plan to program some features they had on their old custom-made-scheduler into Asprova. They believe that they can utilize Asprova to achieve maximum efficiency level.
Data Volume | |
---|---|
Finished products | 600 |
Total items | 700 |
Resources | 29 |
Processes | 2 |
Scheduling period | 3 months |
Scheduling cycle | twice/month |
Lots in scheduling period | 1500 |
Jobs in scheduling period | 1,850 |
Single rescheduling time | 5 seconds |
Japan Polyolefins Co., Ltd.
Since establishment, Japan Polyolefins has been manufacuting and distributing low and high density polyethylene, advanced polyethylene, advanced resin, etc. for home appliances as well as medical supplies.
Left to right: |
Chooses Asprova for Processing Speed Now, Only One Person is Responsible for Two Factories’ Scheduling Work Read More… |
![]() |