Case Study 6 : Metal Manufacturer
Metal Manufacturer Chooses Asprova For Scheduling Speed
Reduces Scheduling Time and Scheduling Cycle Time
-Hitachi Metal, Inc., Kuwana Factory –
The Kuwana factory of Hitachi Metal, Inc. primarily manufactures plumbing system parts for gas pipes, drainage, water supply, fire hose, etc. Before using Asprova, a mainframe computer was used for scheduling, but it took a lot of time and unnecessarily put heavy workload on scheduling managers and on-site workers. On top of that, there was a need to reduce scheduling cycle to meet customers’ needs. After introducing Asprova, they were able to reduce their scheduling time to about 3 hours, and cut schedule cycle time from 1 cycle per month to 1 cycle per week. In addition, with the added functions of Asprova’s COM interface, rescheduling workload was also reduced.
Problems Prior to Introduction
- Lengthy 3 to 4 days schedule drafting time, caused by mainframe computer’s long processing time
- Inflexibility of mainframe computer to sudden order changes, leading to tedious manual calculation and direct on-site adjustment
- Extra workload for on-site workers
- One-month base scheduling that cannot meet customers’ needs
Reasons for Introducing Asprova
- Asprova’s fast scheduling speed
- Asprova’s user-friendly GUI
- Asprova’s diverse master settings
Benefits of Introduction
- Not only reduced scheduling time to 3 hours but cut scheduling cycle to once a week.
- Simplified rescheduling work, as a result of Asprova’s fast scheduling speed.
- Shortened order-to-production lag time, resulting in improvement of response to customer needs.
- Reduced schedule correcting workload, through development of Asprova peripheral functions such a plugins and automation.
Scheduling With Mainframe Computer Began to Show Its Limitations
Until recently, the Kuwana factory of Hitachi Metal, Inc had been using a mainframe computer to make a schedule on a monthly basis. Usually the main computer had to be run at night, as it takes 5 to 6 hours of machine calculation for a scheduling job, and on the next day, 5 schedule managers usually spend a day making corrections to match delivery times, setups, and machine operation time. This cycle would then be repeated several times, so it would take about 3 to 4 days to do one scheduling job. In cases where there was a sudden change in orders, since the mainframe computer is not flexible enough to respond to it, the calculation results would be modified manually, and in many cases direct adjustment at the production site were needed. On more complex adjustment processes, on-site workers would need to cooperate, thus adding workload outside scheduling team. Moreover, monthly basis scheduling was proven to be ineffective in answering customers’ needs, so it was also necessary to reduce cycle time. To deal with these problems, introduction of a scheduler was considered.
On the basis of package selection, Hitachi Metal, Inc.’s Production System Research Department recommended Asprova. The department did compare various production management programs before choosing Asprova. As Hiroaki Simizu of Production System Research Department says, “After attending a lot of seminars and evaluating different packages, I was attracted by Asprova’s speed.” And after trying Asprova’s trial package, they decided to recommend Asprova based on its diverse master settings, user-friendliness of its GUI, and the ability to specify alternate machines.
When implementing Asprova, “we spent time checking interface between the output result and the existing POP system,” said Kenichi Masita, Chief of Factory Manager, Kuwana Factory. The check was done together with on-site production staff, and the system managers also got down on production floor to familiarize themselves with the production site situation. This cooperation between the system department and on-site workers was the key to the successful introduction of Asprova.
Surprising Benefits
Before introducing Asprova, there was a target to transmit data once per week from the mainframe computer. The plan was to improve it first to a one-per-month level, and than progress to the one-per-week goal. However, changes in facility conditions delayed this process. But to everyone’s surprise, Asprova was useful in simulating changes in the facility condition.
After introducing Asprova, the time it takes from scheduling to instruction output decreased to a mere 3 hours. The weekly data transmission from the mainframe computer was also put into practice. And since rescheduling can be done in no time using Asprova, repeated rescheduling is much less exhausting than before. Customer satisfaction has also improved, as a result of the reduction in order-to-production lag time.
Extend Asprova’s Function on Their Own. Reduce Rescheduling Workload.
Hitachi Metal’s employees are extending Asprova’s functionality on their own using technologies including COM interfaces, plugins, and Microsoft Excel. This has reduced the workloads of schedule managers and on-site workers. Furthermore, they have prepared a system for gathering information on common modification and reflecting them in Asprova’s lot priorities and scheduling parameter settings to improve the accuracy of the schedule.
In the future, the factory aims to transmit data on a daily basis from the mainframe computer, cut scheduling time to 1 hour, reduce lead times and setup times, and decrease inventory by 20%. The way to do this is to effectively use Asprova along with its peripheral functions, while synchronizing the system and the production line.
Figure 1: System Configuration
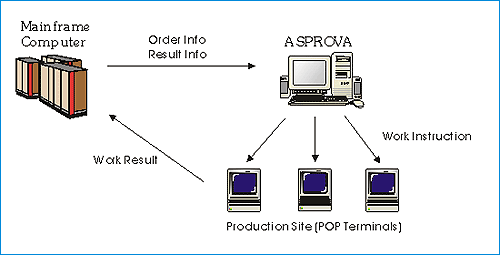
Order information and production result data are transmitted once a week to Asprova’s PC from the mainframe computer. The schedule will then be set to POP terminals at the production site. Production result data is inputted from POP terminals at the production site and set back to the mainframe computer.
Figure 2: Personalized screen of Asprova and a plugin

Schedule can be checked and modified while verifying items’ detailed information.
Figure 3: The company made a utility on their own using Excel to enable every manager to check and adjust Asprova’s schedule

The adjusted schedule is sent back to Asprova through COM.
Figure 4: Main menu of production schedule

A range of demands from the production site is reflected. Asprova’s processing can be executed automatically using the automation function.
Data Volume | |
---|---|
Finished products | 9,000 |
Total items | 60,000 |
Resources | 900 |
Processes | 15 |
Scheduling period | 2 months |
Scheduling cycle | once a week |
Lots in scheduling period | about 20,000 |
Jobs in scheduling period | about 150,000 |
Single rescheduling time | about 15 minutes |
Hitachi Metals, Inc., Kuwana Factory
Since its establishment, the factory has primarily been manufacturing plumbing parts for gas pipes, drainage, fire hose, water supply system, etc., as well as air conditioners, water supply machines, and precision instruments. Following the diversification in material and process needs recently, the factory is doing R&D on new technologies and materials, such as polyethylene pipe system and metal diaframe bulb.
Left to right: |
Chooses Asprova for its high speed scheduling Reduces scheduling time and schedule cycle time Read More… |